Recognizing the Fundamentals and Applications of Plastic Extrusion in Modern Manufacturing
In the world of modern production, the technique of plastic extrusion plays a crucial role - plastic extrusion. This detailed process, entailing the melting and shaping of plastic through specialized dies, is leveraged throughout various markets for the creation of diverse items. From vehicle components to durable goods product packaging, the applications are large, and the capacity for sustainability is similarly impressive. Deciphering the principles of this process reveals the real adaptability and potential of plastic extrusion.
The Fundamentals of Plastic Extrusion Refine
While it may appear complex, the fundamentals of the plastic extrusion procedure are based on fairly simple principles. It is a production process wherein plastic is thawed and then formed into a continuous account with a die. The plastic extrusion process is extensively utilized in various sectors due to its cost-effectiveness, flexibility, and effectiveness.
Various Kinds Of Plastic Extrusion Techniques
Structure upon the standard understanding of the plastic extrusion process, it is essential to explore the various methods entailed in this production technique. The 2 primary methods are profile extrusion and sheet extrusion. In account extrusion, plastic is thawed and formed into a constant profile, commonly utilized to develop pipes, poles, rails, and window structures. On the other hand, sheet extrusion develops large, level sheets of plastic, which are normally further processed into products such as food packaging, shower curtains, and cars and truck components. Each strategy requires specialized machinery and accurate control over temperature and pressure to make sure the plastic keeps its shape throughout cooling. Recognizing these techniques is key to utilizing plastic extrusion successfully in contemporary manufacturing.
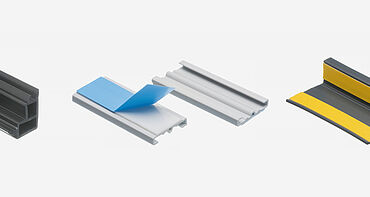
The Duty of Plastic Extrusion in the Automotive Market
A frustrating bulk of components in modern-day cars are products of the plastic extrusion process. Plastic extrusion is mostly used in the production of numerous car parts such as bumpers, grills, door panels, and dashboard trim. Hence, plastic extrusion plays a pivotal duty in vehicle manufacturing.

Applications of Plastic Extrusion in Durable Goods Manufacturing
Beyond More Help its significant effect on the automotive industry, plastic extrusion shows equally effective in the world of customer items producing. The flexibility of plastic extrusion enables makers to design and generate intricate forms and sizes with high precision and efficiency. The adaptability, versatility, and cost-effectiveness of plastic extrusion make it a favored option for several consumer products suppliers, adding considerably to the sector's development and innovation.
Environmental Effect and Sustainability in Plastic Extrusion
The prevalent usage of plastic extrusion in making invites scrutiny of its eco-friendly implications. As a process that often uses non-biodegradable materials, the ecological effect can be substantial. Energy usage, waste production, and carbon discharges are all worries. Nonetheless, sector innovations are raising sustainability. Efficient equipment reduces energy use, while waste management systems recycle scrap plastic, reducing raw product needs. Additionally, the advancement of naturally degradable plastics click reference offers a much more ecologically friendly option. In spite of these renovations, additionally technology is needed to alleviate the environmental impact of plastic extrusion. As society leans towards sustainability, makers have to adjust to continue to be sensible, emphasizing the significance of continual research and innovation in this area.
Conclusion
Finally, plastic extrusion plays a crucial duty in modern production, specifically in the automotive and durable goods markets. Its flexibility enables the production of a variety of elements with high accuracy. Its possibility for recycling and advancement of eco-friendly materials offers an appealing method towards lasting practices, thus attending to environmental problems. Understanding the basics of this procedure is essential to enhancing its benefits and applications.
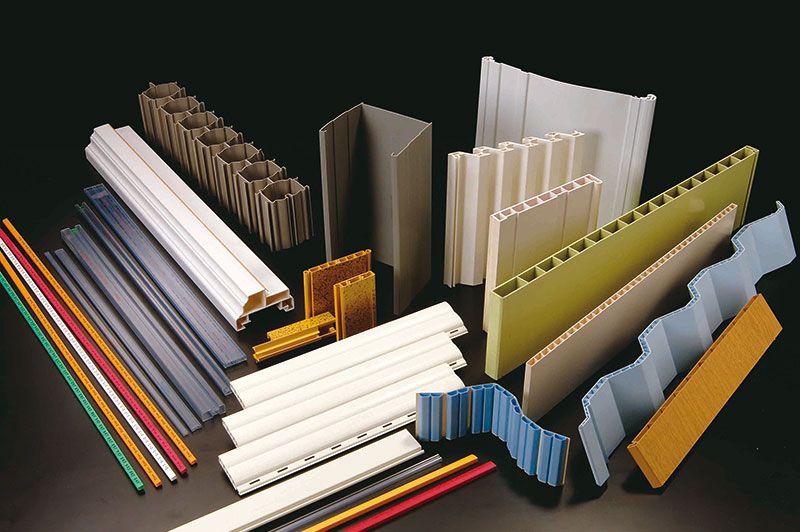
The plastic extrusion procedure is extensively made use of in numerous sectors due to its effectiveness, cost-effectiveness, and flexibility.
Building upon the basic understanding of the plastic extrusion procedure, it is essential to explore the various strategies involved in this manufacturing approach. plastic extrusion. In contrast, sheet extrusion develops huge, flat sheets of try this plastic, which are typically additional refined into items such as food packaging, shower drapes, and cars and truck parts.An overwhelming bulk of parts in modern automobiles are products of the plastic extrusion process